Инженерный пластик
Инженерное компаундирование пластмасс в основном включает в себя двухшнековый экструдер, который может применяться в различных ситуациях.
Серийный экструдер USEON SAT-X с высокомоментным редуктором специально разработан для этого применения.
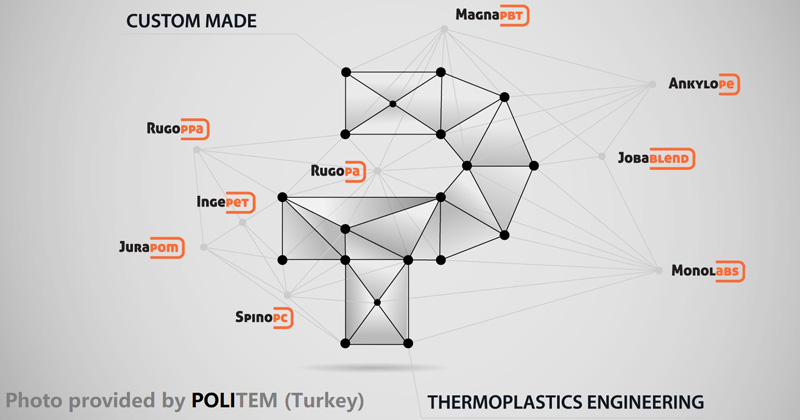
Оглавление
Основная формула
Инженерные пластики общего назначения | Современные инженерные пластики | Добавки |
---|---|---|
PA6, PA66, PA46, PPA | PBI | Стекловолокно |
ABS | PAI | Углеродное волокно |
POM-C, POM-H | PEEK | Огнестойкость |
PET | PPS | УФ-стабилизатор |
PC | PEI | Антиоксидант |
PBT | PSU | Антистатический |
PE-(U)HMW | PVDF | Цветной пигмент |
Применения
- Автомобильные (Впускные коллекторы, баки для коллекторов, фильтры, вентиляторы и кожухи, крышки двигателя и т.д.)
- Электрические (клеммные колодки, кабельные стяжки, разъемы, электроинструменты, MCCB, реле, освещение и т.д.)
- Выдувное формование (медицинская и косметическая тара, тара для смазочных материалов и краски и т.д.)
- Экструзия пленки и труб (BOPA, BOPET, PET лист, трубы и т.д.)
- Волокно (PA волокно, PSF, FDY, PSF и т.д.)
- Прочие промышленные товары (строительство, товары для дома, мебель, игрушки и т.д.)
Переработка инженерного пластика
Инженерный пластик чувствителен к перегреву и гидролитическому разложению.
Наш серийный экструдер SAT-X с удельным крутящим моментом 13 Нм/см3 и скоростью 800 об/мин может обеспечить более высокую производительность при меньшем времени пребывания, лучшую дисперсии и более точный контрольтемпературы.
a) Технические характеристики экструдера
Модель | Диаметр (мм) | Макс. Скорость (об/мин) | Мотор (кВт) | L/D | Производительность (кг/час) |
---|---|---|---|---|---|
SAT-X52 | 51.4 | 800 | 160 | 40-44 | 450-700 |
SAT-X65 | 62.4 | 800 | 280 | 40-44 | 750-1200 |
SAT-X75 | 71.4 | 600 | 355 | 40-44 | 850-1500 |
b) Система отопления
Вместо традиционного литейного нагревателя (снаружи цилиндра) мы используем картриджный нагреватель (производства Германии) внутри цилиндра, что позволяет экономить энергию. Полимер будет плавиться в основном за счет нагрева, а не месильных элементов, поэтому срок службы шнека и цилиндра больше, а качество компаундирования выше.
c) Система охлаждения
Два входа и выхода на каждом цилиндре обеспечивают более равномерное и быстрое охлаждение.
d) Опорная рама
Точка опоры традиционного цилиндра находится внизу. При нагревании его тепловое расширение увеличивается до 0,2~0,5 мм (разница в зависимости от размера экструдера), и возникают неравномерные зазоры в верхней и нижней части между шнеком и цилиндром.
Точка опоры цилиндра экструдера SAT находится посередине. При нагревании тепловое расширение равномерно направлено вверх и вниз, обеспечивая высоту центра на горизонте и образуя равномерные зазоры в верхней и нижней части между шнеком и цилиндром.
e) Система подводного стренговой грануляции
Стренги автоматически попадают в гранулятор под действием потока воды, даже стренги ломаются во время замены фильтра. Таким образом, отходов в процессе производства практически не будет.
Если количество стренг превышает 25 штук (производительность около 800 кг/ч), оператору будет труднее подавать горячую стренгу в гранулятор вручную.
Несколько различных методов переработки
1) Компаундирование короткого армирующего волокна
Добавьте ровинговую форму или измельченное стекловолокно в двухшнековый экструдер непосредственно и соедините с полимером, и вы получите гранулы длиной 4 мм с длиной стекловолокна 0,2~0,3 мм.
a) Ровинговое стекловолокно
Расположите 20 кусков ровингового волокна на опорной раме с весовым преобразователем – Mettler Toledo.
Поместите волокно в вентиляционное отверстие на пятом цилиндре. Они будут забираться в цилиндр двухшнековым экструдером.
С весовым контроллером для индикации скорости подачи (кг/ч). Вы можете регулировать производительность подачи путем увеличения/уменьшения скорости шнека или количества волокон.
b) Измельченное стекловолокно (длиной 4~6 мм)
Feed into the fifth barrel by two stage side feeder:
The top stage is loss-in-weight feeder with output control.
The bottom stage feeder works with fixed speed for force feeding.
2) Длинноволокнистый термопластик (LFT)
Детали из LFT обычно изготавливаются с использованием одного из трех различных методов обработки, как показано на рисунке 1.
① Экструзионная линия для производства термопластичных однонаправленных лент (UD-лент)
Добавьте стекло/углеродное волокно в форме ровинга в Т-образную фильеру,, затем покрытие плавящимся полипропиленом PE/PP/PET из экструдера. Вы получите лист шириной 610~1220мм и толщиной 0.25~0.4мм. Он используется для стеновых панелей зданий, грузовиков/прицепов.
- Для листового материала из ПП подходит одношнековый экструдер.
- Для PA/PET базового листа, это должен быть двухшнековый экструдер.
Материал: PP/PE/PET/PA, мастербатч, ровинг из углеродного/стекловолокна 50~60%.
Экструдер: SAT40 или SAT52 двухшнековый экструдер
Эффективная ширина: 610 мм или 1220 мм
Толщина и диапазон допусков: 0.25~0.35мм, +/- 0.02мм
Скорость линии: 6-12 м/мин
Описание технологической схемы:
Устройство поворота стекловолокна → тяговый блок → гравиметрический смеситель периодического действия → весовой дозатор → двухшнековый экструдер → фильтр расплава → погружная матрица → система калибровки давления → охлаждающий штабель и обрезка кромок → намоточное устройство
② LFT-G (длинноволокнистый термопластичный компаунд для непрямого формования)
Добавьте стекловолокно в форме ровинга в форму для пропитки, затем покройте его плавящимся полипропиленом (PP) из двухшнекового экструдера. Вы получите гранулы 6-16 мм с одинаковой длиной стекловолокна внутри. Гранулы могут быть использованы для производства любых изделий с помощью литьевой машины.
Модуль упругости LFT-G в два раза выше, чем у термопластика, армированного короткими волокнами, а ударное напряжение в четыре раза выше, сохраняя свои функции без изменений при температуре минус -30°C.
③ Технология прямого LFT
Предполагает соединение сырья (волокна и матрицы) непосредственно перед поступлением в формователь и позволяет избежать получения промежуточного продукта. Это дает производителю возможность улучшить свойства смолы в соответствии с требованиями применения путем добавления наполнителей, антипиренов и добавок, а также значительно снизить затраты на материалы и создать только одну тепловую историю матрицы. Этот прямой процесс можно разделить на два процесса:
LFT-D-IMC (процесс литья под давлением длинноволокнистых термопластов)
Расплавляет полимер и смешивает его с волокном, присоединяется к машине для литья под давлением.
LFT-D-ECM (экструдерное компрессионное формование длинноволокнистых термопластов)
Использует две системы экструдеров для плавления полимера и дозирования волокна в сочетании с гидравлическим прессом для компрессионного формования.
Существует два основных преимущества LFT-D-ECM перед двумя другими технологиями.
Во-первых, этапы компаундирования и смешивания волокон разделены, поэтому оба экструдера могут быть индивидуально оптимизированы для выполнения своих специфических функций.
Во-вторых, материал не подвергается таким высоким уровням напряжения, как при литье под давлением, что помогает сохранить длину волокна. Это очень важно, так как механические свойства термопластов, армированных волокном, сильно зависят от длины волокна. Таким образом, процесс LFT-D-ECM дает максимальную степень свободы в плане оптимизации выбора материала, модификации полимера и параметров процесса, что очень важно для автомобильной промышленности.
Проекты / Клиенты
Двухшнековый экструдер для компаундирования ПА + стекловолокна, Taisu в Китае
Линия компаундирования PA66+45% стекловолокна, Taisu в Китае
Компаундирование LFT-G для непрямого формования (двухшнековый экструдер SAT40)
Компаундирование LFT-G для непрямого формования (двухшнековый экструдер SAT52)
Компаундирование LFT-G для непрямого формования (двухшнековый экструдер SAT75)
LFT-D-ECM (компрессионное формование длинноволокнистых термопластов в экструдере)
Линия по производству термопластичных композитных лент, армированных непрерывным волокном